My readers know that I always talk about my 40 years in this engineering business solving process filtration and drying problems. Most recently I used this knowledge in my P&ID consulting for Diemme Filter Press Technology, a brand of the Aqseptence group. I wrote a paper entitled “Process Testing for Improving and Optimizing the Solvay Sodium Carbonate Production Process with Filter Press Technologies.” The paper focuses on calcium carbonate/calcium chloride waste product initially discharged into the ocean. Using Diemme® Filtration filter press technology the client eliminated this environmental problem and created a salable product.
Discharging calcium carbonate / calcium chloride waste product into the sea created an environmental problem for the site. In addition, the calcium chloride waste represented lost revenue as the product has value for salt de-icing of roads, sidewalks, etc. in cold weather climates. The client contacted Diemme® Filtration to conduct laboratory test work to determine the optimum solid-liquid filtration technology to produce high-quality calcium chloride.
Testing Leads to Filter Press Technologies Improvements
The solution called for a two-step process. First, the calcium carbonate is filtered and dewatered. The dewatered cake is discharged to conveyor belts into a crusher and then into a downstream mix tank. There, cake is mixed with water and dissolved with hydrochloric acid to produce the final calcium chloride in liquid form. The calcium chloride liquid is filtered again before evaporation to produce the final product.
For the first slurry, testing showed excellent filterability with granular crystals forming a compact and homogenous cake. The well-formed cake discharged completely from the polypropylene filter cloths. The scale-up is based upon testing using membrane plates with a chamber/cake thickness of 50 mm. The sizing resulted in two (2) GHT 1200 x 1200 overhead beam-high performance filter presses with a filtration area of 210.24 m² each. The GHT 1200 has 46 membrane plates with 50 mm chambers and a total volume of 4,428 liters.
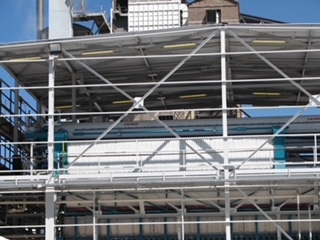
For the second final product slurry, additional testing was conducted. In this case, the slurry contained magnesium as a precipitated magnesium-hydroxide. This slurry needs filtration to remove the hydroxides from the CaCl2 liquid before it can be evaporated, concentrated, and stored in big super sack bags. The scale up for this part of the process resulted in one (1) ME 1000 x 1000 side beam-versatile performance filter press with a filtration area of 36 m². The ME 1000 has 24 membrane plates with 20 mm chambers and a total volume of 1,000 liters.
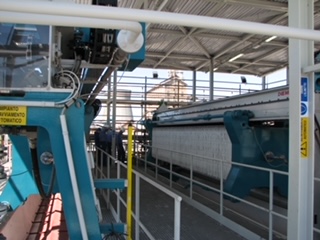
Continuous Optimization
Diemme® Filtration provides continuing process support for their clients. As a result, after 18 months of operation, the client upgraded the process. Cake washing was incorporated into step 1 of the process to reduce the chloride concentrations to below 5 g/kg of cake. From the washing tests, the process was further optimized to reduce the chlorides to 0.62 g of Cl per kg of cake with a low wash ratio of only two chamber volumes.
The installed Diemme® Filtration Filter Press technologies in Figures 1 and 2 provided significant improvements for the client’s Solvay process. The most important is attaining a more sustainable process. Further, Diemme® Filtration has helped the client produce a high-quality product that generates revenue.
You can download the full paper and contact me for more information. P&ID can provide materials for your organization including white papers, market research, and case studies to increase your market penetration.