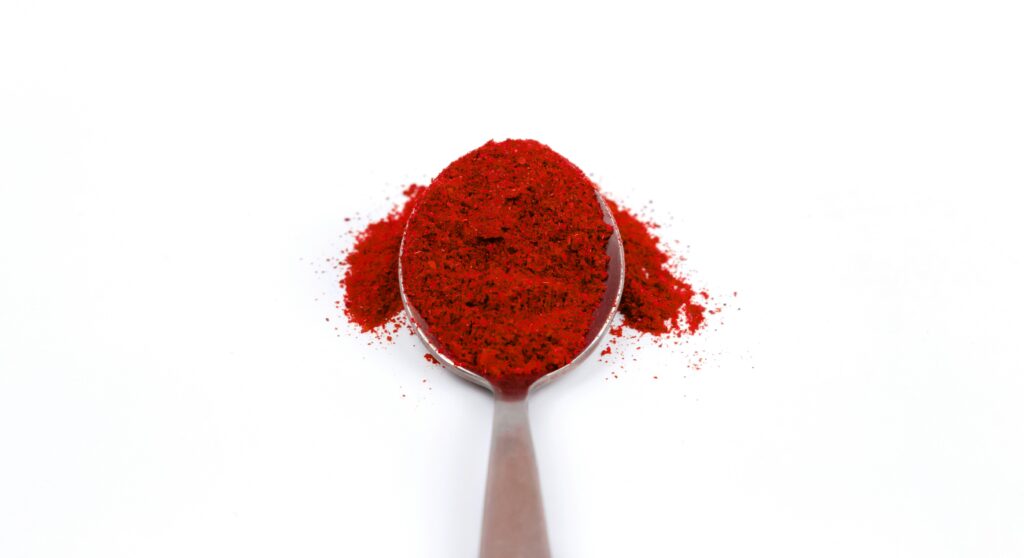
The drying process is fundamental in solids process engineering. The term “drying” usually refers to the thermal removal of a liquid from a solid product. The mechanical solid-liquid separation process is not considered as “drying,” but rather “dewatering.” Over time, the trend has developed to expand the use of dryers for mixing, cooling, stripping, reacting, crystallizing, extracting, and evaporating. This topic is also highlighted in my book, “Integration and Optimization of Unit Operations” in chapters 7 and 8, where there is a full description of dryers and filter-dryers.
As an overview, process dryers can be segmented initially as batch or continuous:
Batch dryers
- Tray dryers
- Spray dryers
- Rotary dryers
- Vertical Vacuum dryers
- Pan dryers
- Spin Flash dryer
- Horizontal paddle dryers
- Cone/Tumble dryers
Continuous dryers
- Conveyor dryers
- Belt dryers
- Fluid bed dryers
- Spray dryers
- Horizontal paddle dryers
- Tunnel dryers
- Rotary dryers
Simplifying Dryer Selection
With so many choices and options to consider, it’s best to make your decision based upon lab and pilot testing. Robust data collection, drying curves and heat balances are needed to land on the optimum design for chemical/pharmaceutical materials manufacturing. P&ID can assist with this process.
Typical questions in selecting a dryer technology for solids process engineering include:
- Dryer throughput, mode of feedstock production (batch/continuous), turndown ratio and flexibility in capacity requirements
- Physical & chemical properties of the wet feed and final product specification including moisture content of the feed and product (Wet and Dry basis)
- Variability in feed characteristics and process parameters
- Toxicological properties of the product
- Upstream and downstream processing operations
Troubleshooting for Solids Process Engineering
Once the dryer technology is selected, installed, and started-up, you might get the dreaded Saturday midnight telephone call that the dryer is not working. Of course, the only information that you get is the cycle times are long, the throughput is low, or the moisture content is above the “bone-dry” specification.
Before you get dressed and go to the plant ask the following questions:
- Is there a mass balance which would include material flow rate, moisture content, air flow rates, etc.?
- Are the upstream and downstream components working correctly and secondly are the instruments calibrated correctly?
- What are the product observations: balling, agglomeration, or cracking?
- What are the dryer observations: vacuum level, temperature levels, gas flow rates, product sticking to the walls, or product not discharging?
If you can get all this information via e-mails or texts, great. You may be able to provide a solution and go back to bed. Still, you’ll likely want to “go and see for yourself” (although maybe it can wait until Monday morning). In my experience, no matter how good the information may seem to be, firsthand knowledge is fundamental to do your best work. Following the MBWA (Management By Walking Around) principle, will help you keep thinking, asking questions, and innovating.
Good luck and, please, feel free to contact me with your dryer selection and troubleshooting questions.