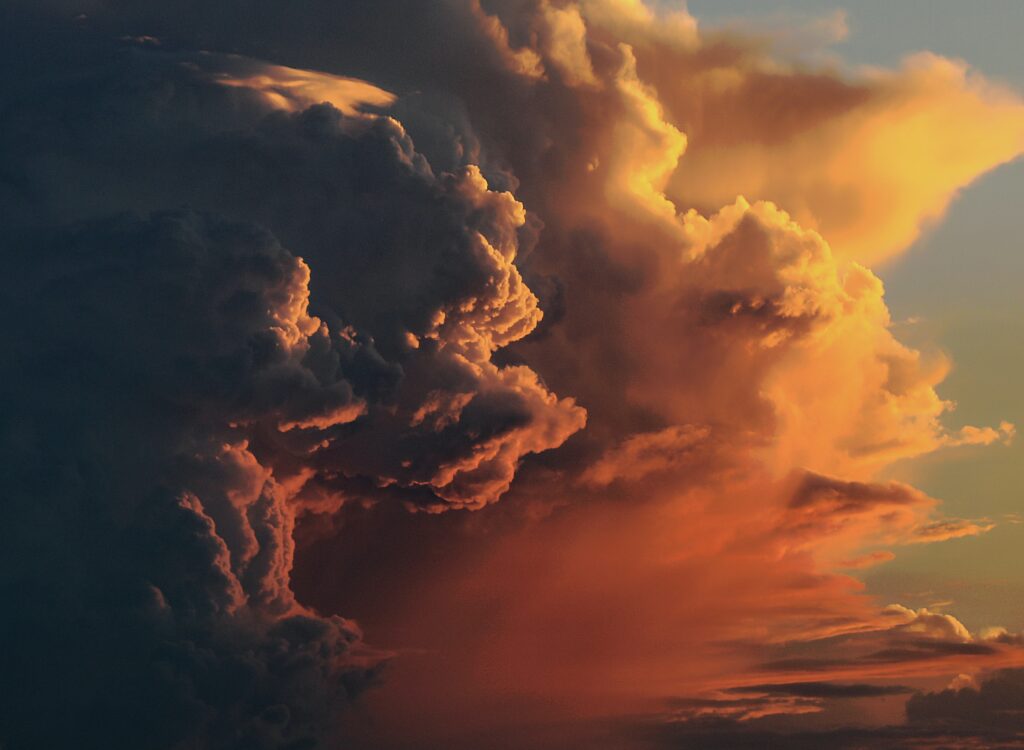
This is an edited version of an article I wrote for The Chemical Engineer. I hope you enjoy this take on automated clarification technologies.
Throughout my career in the solid-liquid separation market space, I have seen some interesting solid-liquid separation solutions. At one melamine resin facility, the slurry was in a formaldehyde process. The operators were wearing masks, opening up a manual plate filter in a room with residential floor fans, to dig out the cake from the paper filter media.
In another case for zeolites, the client had multiple bag filters to clarify the filtrates following a vacuum belt filter. When the filtrates, the final product, remained cloudy, to my surprise, the client decided to add another set of bag filters!
A clarification system is employed after coarse-particle filtration or as a stand-alone system to remove fine particles at low concentrations. These particles are typically less than 5 µm and are in concentrations less than 5% solids down to ppm levels.
Process engineers struggle to clarify process liquids. But there are ways to automate the clarification processes to improve filtration and minimize operator exposure. The cake solids structure and the nature of the process will determine which types of pressure-filtration, automated clarification technologies are best for you.
Candle Filters
A candle filter is a pressure vessel filled with tubular filters (called filter candles). A typical filter candle comprises a dip pipe to flow the filtrate and pressurized gas, a perforated core with supporting tie rods, and a filter sock.
As the cake builds during operation, the candle filter’s removal efficiency increases, enabling removal of particles as small as approximately 0.5 μm.
During operation, a feed pump or pressure from the reactor or feed tank forces the slurry into the bottom of the pressure vessel. The solids build up on the outside of the filter sock, while the liquid filtrate flows into the candle, through the registers, and out of the vessel. This process continues until the maximum pressure drop, design cake thickness, minimum flow, or maximum filtration time is reached. The cake is washed to remove impurities and residual mother liquor, and then dried by blowing gas through the cake. Next, low-pressure gas enters the individual candles and expands the filter socks.
This process breaks apart the dry cake, which detaches from the filter sock and falls into the vessel cone. Candle filters are used for thin-cake (5–20 mm) pressure filtration applications. They are best suited for filter cakes that are vertically stable.
Pressure Plate Filters
Like the candle filter, pressure plate filters comprise filter elements contained within a pressure vessel. However, instead of vertical filter candles, the vessel containshorizontal filter plates. These elements are slightly sloped, conical-shaped metal plates that support a coarse-mesh backing screen covered with filter cloth.
An opening in the centre of the plate allows the filtrate to travel between plates and throughout the vessel. The filter cloth can be synthetic, as in the candle filter, or metallic as the cake discharge is by vibration or spinning.
Operation is similar to that of a candle filter. For cake discharge, there are two main designs. In one, two unbalanced motors vibrate the filter plates to dislodge the cake from the filter cloth. In a second design, the plates spin so that the cake can be ‘thrown’ off the plates. Pressure plate filters are used for filtration of cakes up to 75 mm thick.
Sintered Porous Metal Cartridges
Another type of automated clarification technology is based upon sintered porous metal cartridges. These can be used in a variety of process flows such as inside-out filtration. After each cycle, solids are backwashed off the inside of the elements and discharged as a concentrated slurry or wet cake. They can also operate in a conventional outside-in filtration. Porous metal cartridges are used for high temperature applications greater than 200oC where the solids are well-defined hard crystalline shaped.
Filter Aids
Filter aids are generally the last resort. Often in clarification applications, the solids are very fine or amorphous, so can be difficult to filter. When filtered, the solids will create a thin, impermeable coating over the filter media and immediately reduce the filtration rate to an unacceptable level. In these difficult cases, filter aid pretreatment can be used to improve filtration properties and efficiently remove the fine solids from the process liquids. The types of filter aid include diatomite, perlite, and cellulose.
In the precoat method, filter aid is used to generate a thin layer of solids on top of the filter media. Once formed, the filter aid cake functions as the primary filter media. Therefore, the filter cloth is no longer the real filter when precoat is used. For that reason, the filter cloth should be as open as possible while still retaining the filter aid material.
The precoat process is achieved by mixing the filter aid into clear liquid or mother filtrate in a precoat tank. This slurry is then recirculated through the filter where the solids are captured by the filter media. The clean filtrate is recirculated back into the precoat tank. The precoat should be thick enough to ensure that the entire media surface is coated but thin enough so that it does not provide significant resistance to filtration.
In body feed filtration applications, the filter aid is blended with the slurry feed either by dosing the concentrated filter aid suspension into the slurry feed with in-line mixing or by mixing the filter aid into the entire slurry batch and maintaining agitation. By adding filter aid into the slurry feed, the resulting filter cake is more porous, allowing higher and longer sustained flow rates. Body feed also helps to restrict solids movement which improves filtrate clarity.
Needless to say, the use of filter aid improves filtration but requires more equipment, more process control, and results in more solids for disposal.
Final Thoughts on Automated Clarification Technologies
How can the process engineer be successful? When confronted with a clarification process, don’t simple throw more bag filters at the problem. Conduct lab testing to analyze the cake structure, filter media, filtration pressure and cake thickness. With the data in hand, you can evaluate the different technologies and design a more reliable and cost-effective clarification process. Find a different approach!
1 Comment
Comments are closed.
Greetings Barry…thanks for sharing, congrats on your accomplishments up to now….Best of Health to You and Love Ones ..JG