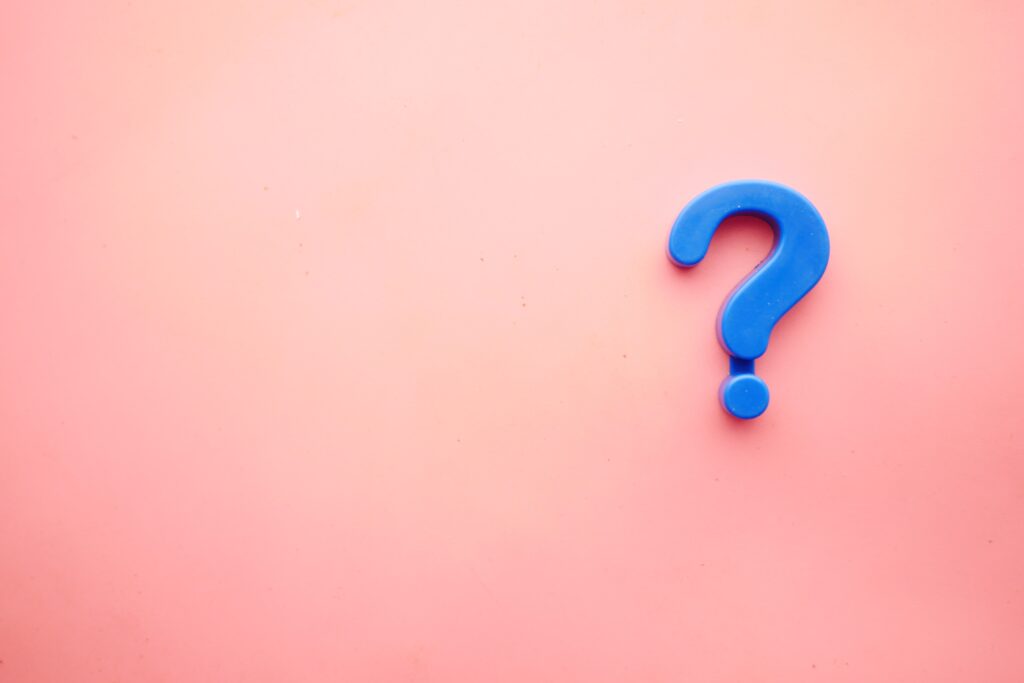
In past blogs, I’ve talked about reactive and proactive process troubleshooting. Reactive troubleshooting requires quick action to look at mechanical issues, upstream and downstream equipment, and operational procedures. In proactive troubleshooting, we ask probing questions and walk around the plant to uncover potential problems and offer solutions.
Dirk Willard, Contributing Editor of Chemical Processing, in his recent article “Read and Think Critically” offered more to think about on this subject.
Dirk used an example of trying to write a debottling report and discovering several missteps:
- The product manual was poorly written
- The plant engineer had not identified what was missing from the manual and what he didn’t understand
- No logic was applied to decide who would know best how to run the equipment — “the engineer who built it or the process expert who operates it”
- The engineer could have paid more attention to the section that was more detailed on the topic at hand.
Ultimately, what was missing? Critical thinking! He called for “questioning the value of information, its relevance and validity, the agenda of the source and, most importantly, the logic on which the data are based.”
He offered real world examples of critical review, “identifying what’s being done, how it’s done, why it’s done, and who’s doing it” with a paper mill selecting a close-coupled water pump without considering all angles of the decision.
Take a Critical Approach to Process Troubleshooting
I bet you can easily add your own examples. For instance, there always seems to be a question about instrument and compressed air for the process. The process design for valve actuation has one pressure, but the operators know that in normal operation there is high demand. So the instrument air pressure drops and the valve actuates more slowly. Slow actuation results in lower production. Thus, we need to keep in mind the actual conditions versus the design conditions.
As for compressed air, it used to be “free” at the plant. Not any more. Every plant now considers this a cost of operation. Once again, operators know that during high demand, the air pressure drops. But the process designers may not have considered this. Next time, design in a compressed air tank so that your process can meet the requirements.
To do your best work, keep thinking, keep reading, and keep asking questions. If you have an area of expertise, let me know; I am always learning and maybe I can use your skills. I’m always interested in learning more about process troubleshooting.