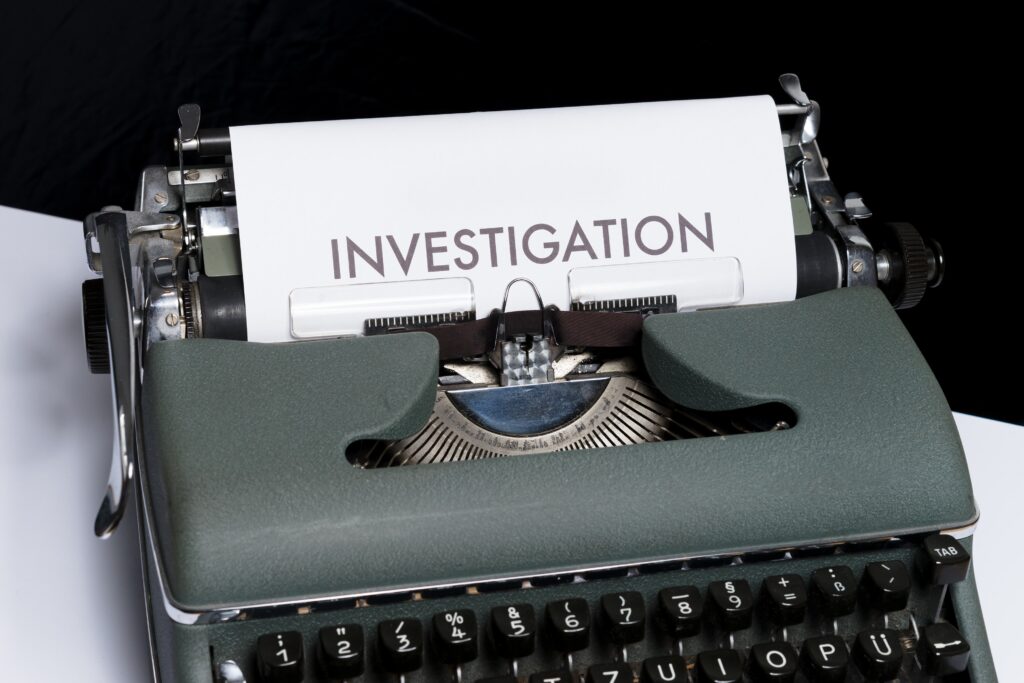
For years, my focus as a process engineer has been thin-cake filtration, cake washing and drying technologies. I am continually engaged by the people I work with and the ongoing need to find new process solutions to problems.
There are always new challenges. Our latest BHS Sonthofen newsletter focused on practical solutions for solid-liquid separations in chemical and pharmaceutical applications. Particularly, this issue of Art and Science of Filtration, looked at new clean-in-place (CIP) challenges.
Our friends at CH2M and EI Associates collaborated to examine large-scale fermentation systems in biochemical and biopharmaceutical settings. In discussing designing new organisms to target desired chemical products, they addressed several challenges with genetically modified microorganisms (GMM):
- GMM are not, typically, designed to be robust and can find competition with natural microorganisms difficult.
- GMM are a new creation and can exhibit unforeseen and undesirable traits.
- Incorporating extensive CIP and sterilize-in-place (SIP) systems to prevent contamination is critical.
In discussing considerations for CIP process, the authors focused on sequence, system configuration, equipment sizing, tank and piping design considerations, and more. That’s before they even examined the SIP considerations. It’s not for everyone, but I love trying to fit together the many puzzle pieces to make the process work for our clients.
Also in our newsletter, we shared a CIP presentation from my colleague Tim Ochel. He addresses influencing factors in CIP (velocity, temperature, chemicals, time and technology) and how BHS Filtration meets the need. For instance, BHS’ Rotary Pressure Filter (RPF) is menacing in transforming materials into value. It can handle filtration and washing, multi-step counter-current cake washing, and drying too. He demonstrates how our RPF is successful in applications where optimum cleaning effectiveness, cGMP compliance and contained product handling are required.
There’s a lot to think about when it comes to CIP process in pharma. Another BHS article has talked about the advantages of continuous filtration for pharmaceutical manufacturing. We’re determined at BHS to keep abreast of process design strategy trends to make sure our clients are safe and streamlined while they work to save their customers from whatever ails them.
2 Comments
Comments are closed.
Interesting advances in a difficult area. Are you doing anything in high value food products?
[…] on different ways of approaching particle analysis. The permutations are endless of course as process engineers must address off-line and in-processes and how the particle size and shape impacts the filtration system […]